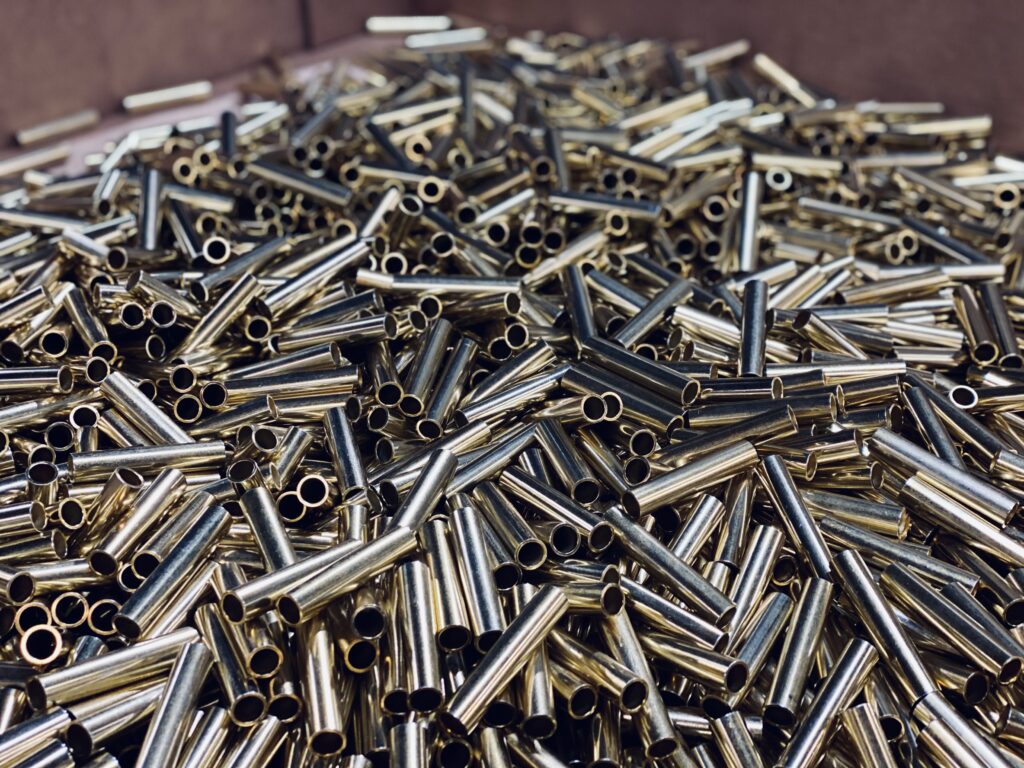
ASTM B633 is a standard specification published by ASTM International that provides requirements for electroplating zinc on iron and steel parts. The standard covers various aspects of the electroplating process, including the composition of the plating solution, the thickness of the coating, and the adhesion and corrosion resistance. It is commonly used in the automotive and construction industries, among others.
ASTM B633 provides several specifications for electroplated zinc coatings on iron and steel parts, including:
- Type of coating: The standard specifies several types of electroplated zinc coatings, including electrodeposited coatings with or without a supplementary chromate treatment, mechanical deposition coatings, and hot-dipped coatings.
- Thickness: The standard provides minimum and maximum thickness requirements for each type of coating, which are measured using appropriate methods such as magnetic or beta backscatter gauges.
- Adhesion: The standard provides requirements for the adhesion of the coating to the substrate, which is determined using methods such as bend, impact, or thermal shock tests.
- Corrosion resistance: The standard provides requirements for the corrosion resistance of the coating, which are determined using methods such as salt spray, humidity, or cyclic corrosion tests.
- Surface preparation: The standard provides guidelines for the surface preparation of the substrate before electroplating, which can include cleaning, pickling, and activation.
- Sampling and testing: The standard provides guidelines for the sampling and testing of coated parts, including the number and size of samples and the acceptance criteria for test results.
ASTM B633 defines salt spray requirements for different electroplated zinc coatings on iron and steel parts. The salt spray test is used to determine the corrosion resistance of the coating. Here are some of the salt spray requirements specified in the standard:
- Type I – as-plated without supplementary treatment: minimum 48 hours to white corrosion, minimum 96 hours to red rust.
- Type II – with supplementary chromate treatment: minimum 96 hours to white corrosion, minimum 240 hours to red rust.
- Type III – with phosphate conversion coating: minimum 72 hours to white corrosion, minimum 120 hours to red rust.
Triplex Plating is capable of meeting a wide range of industry specifications.